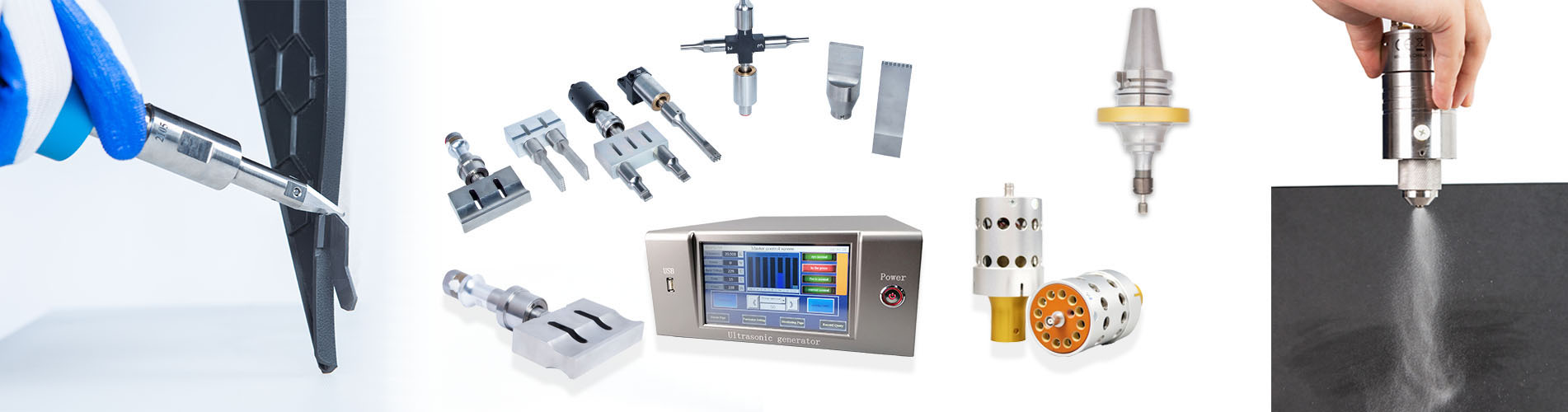
Acoustic frequencies between 16 kHz and 1 GHz are referred to as ultrasound; in industrial settings we call it “ultrasonics”. To clarify: people are able to hear frequencies between 16 Hz and 20 kHz; i.e. the lower frequencies of industrial ultrasonics are audible, especially if secondary frequencies are generated. And what is more, ultrasonics is palpable when touching the weld tool. For ultrasonic welding, the frequency range is between 20 kHz and 70 kHz. Additional fields of application: Imaging ultrasound in the field of medical diagnostics ranges between 1 and 40 MHz. It is not audible or palpable. In the field of industrial material testing, ultrasonics is used at frequencies from 0.25 to 10 MHz.
Payment:
TT, West union, PaypalProduct origin:
ChinaShipping port:
ShanghaiUltrasonic Welding is a Low Stress Process For Components and Makes Complex Component Geometries Possible
Description:
Ultrasonic welding of thermoplastic materials is a weld technology utilizing mechanical vibrations to generate heat due to molecular friction. These vibrations excite the molecules in the plastic so that they start moving. The plastic becomes soft and starts melting. The components are bonded by cohesive or form-fit joints After a short hold time under pressure, they are firmly joined molecularly.
Specifications:
|
Gun Type& Cylinder Type |
||||
Model |
HS-40 |
HS-35 |
HS-30 |
HS-28 |
HS-20 |
Frequency |
40khz |
35khz |
30khz |
28khz |
20khz |
Power |
500W |
500~800w |
500~800w |
500~800w |
500~1000w |
Horn |
≤10mm |
≤10mm |
≤10mm |
≤12mm |
≤13mm |
Housing Diameter |
44mm |
44mm |
44mm |
44mm |
64mm |
Weight of welder |
1.0kg |
1.0kg |
1.0kg |
1.0kg |
1.5kg |
Digital generator |
● |
● |
● |
● |
● |
Analog generator |
● |
● |
● |
● |
● |
Gun type: in accordance with the shape design of human body engineering, ultrasonic start switch is located on the trigger, easy to grasp and use the welding operation, especially suitable for horizontal or vertical.
Cylinder type: for the appearance of design straight, ultrasonic start switch is located outside the cylinder, easy welding and hand carried, can also be installed between the on machine, welding operation for each direction.
How does ultrasonics work?
Ultrasonic vibrations are mechanical longitudinal waves that:
achieve deformation in plastic materials
cause friction between molecules
The resulting friction heat generates a melt that bonds the joining partners within the molecules.
Friction occurs due to impedances in the material, absorption and reflection of the mechanical vibration:
internal friction in the molecule bond = dissipative work
external friction between joining partners = surface friction
Interior:
Ultrasonics is not only suitable for joining plastic materials with each other, but also for joining plastics and other materials, such as metal, or wood. Even chromium components are suitable for ultrasonic staking. By means of sonotrode grouping, it is also possible to realize particularly demanding joining tasks, such as welding of large instrument clusters. Brilliant surface finish and precise gap control is achieved.
Ultrasonic welding: ultrasonic vibration with ultrasonic welding mould, the ultrasonic welding energy conduction to the plastic surface, resulting in local temperature, so that the plastic surface melting. Under the pressure of the ultrasonic hand, so to weld plastic, beautiful, strong effect.
Ultrasonic implants: the nut screws or other metal into plastic work piece. Ultrasonic energy through the ultrasound machine will be transmitted to the metal. The high-speed vibration and heat, the pressure in the ultrasound machine to make metal objects embedded directly into the plastic inside.
Ultrasonic riveting: the nature of metal and plastic or two different plastic bonding together, can make use of ultrasonic riveting machine, so that the weldment hard brittle, beautiful, strong.
Ultrasonic welding: the use of ultrasound machine small welding head, the two pieces of plastic products into multi-point welding, or welding the first row of teeth on a direct pressure on the two plastic work piece, so as to achieve the effect of ultrasonic welding.
Applications In Automobile:
Ultrasonic welding is particularly suitable for:
Joining of injection-molded parts
Embedding of membranes
Embedding of leather, nonwoven materials, and textiles
Staking of different types of materials
Production of form-fit joints by swaging
Inserting of bushes and magnets
Requirements:
Components of Ultrasonic Welding (Horn, Booster and Transducer)
They can amplify the amplitude at a particular ratio step by step. For example, the transducer amplitude is 6mm, the booster can amplify it triply to 18mm, and then the horn can make it to 36mm. However, the work life of horn would be shortened with the amplification of amplitude. The required amplitude differs with the welding material.
There are three common horn material:
1.Titanium
high price, excellent performance good toughness and low loss, difficult to be processed;
Its amplitude can reach to 60mm.
2. Aluminum
low price, fast loss, easy to be processed;
Its highest amplitude less than 300mm.
3. Steel
too hard to be made as horn;
its highest amplitude less than 25mm;
It is suitable for cutting but the blowpipe need to be added in for its cooling.
Previous :
35Khz 1200w Customized Ultrasonic Welder with Multi Spot Dots for Filter CottonNext :
Complete Functionality of Integrated Functional Elements is Ensured in Ultrasonic Welding of Such ComponentsIf you are interested in our products and want to know more details,please leave a message here,we will reply you as soon as we can.
Categories
New Products
© Copyright: 2025 Hangzhou Altrasonic Technology Co.,Ltd All Rights Reserved
IPv6 network supported
Scan to WhatsApp