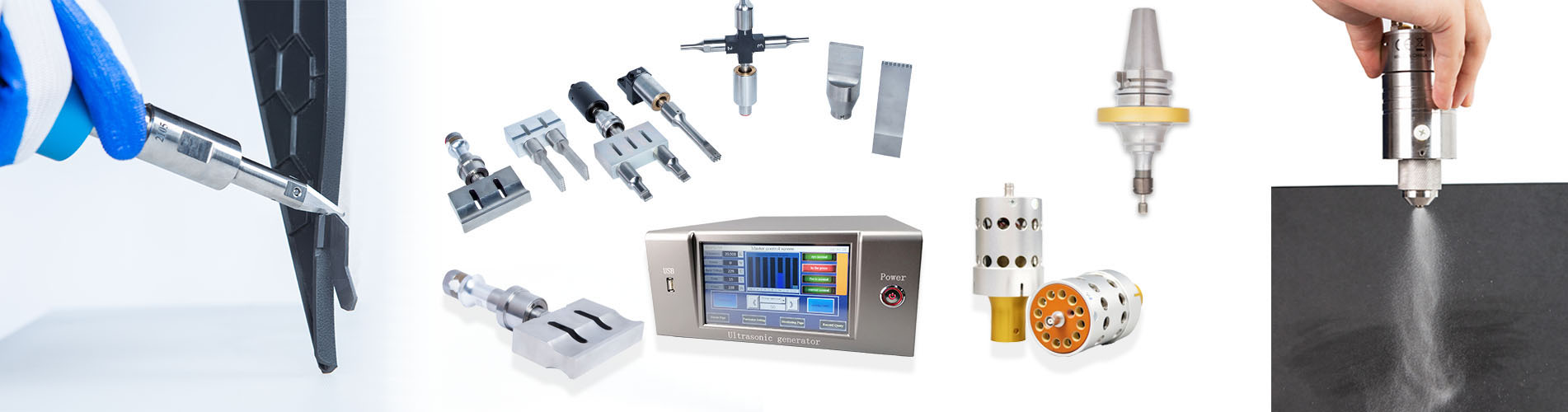
Ultrasonic Welding Used in Electric Vehicles
Functional parts
Ultrasonic welding of these components can ensure that the functions of the built-in functional components are not restricted. All welding parameters can be 100% checked and recorded. The semi-permeable membrane is used as a pressure balance element (DAE), which can be punched and sealed with ultrasonic waves at the same time.
In the car
In addition to the cover and the display screen, electronic components can also be welded and riveted. The use of ultrasonic welding technology can introduce energy into the welding area in a targeted manner to ensure the safe connection of the support plate and the outer cover, and will not pose a threat to sensitive electronic components.
Car exterior/lights
High strength, tightness, dimensional accuracy, and appearance without scratches and indentations are typical requirements. Ultrasonic welding can protect the function of components and complete the welding of complex shapes.
Reliable connection of high-voltage cables for electric vehicles
The motors used in electric vehicles must be able to provide full power output at the moment of starting. This requires reliable connection of high-voltage cables in the car. The cables and plugs connecting the charging pile and the high-voltage battery require reliable low-contact resistance connections to achieve fast charging. This is usually effective welding of copper, aluminum or a combination of the two to achieve the high-voltage cable connection of the vehicle.
Cables with a cross-section of 70, 95 or 120mm must be firmly welded to the high-current connecting piece. The design engineer requires the welding width to be as narrow as possible to save installation space. However, it is difficult to achieve using traditional technology, and now it is easy to achieve reliable connection with ultrasonic welding.
Wire Harness Welding for Electrical Connection of Electric Vehicles
Electric vehicles have fewer moving parts, which greatly reduces maintenance costs and improves reliability. The ultrasonic welding system itself is very reliable and has low maintenance costs. Therefore, when reliable and long-life electrical connections are required to meet the high-quality standards required by the automotive industry, the use of ultrasonic technology for wire connection is the preferred solution.
Ultrasonic wire harness welding has obvious economic and technical advantages: simple process and high cost-effectiveness; low contact resistance; high connection strength. And the welding components are very flexible and easy to integrate into the automated production line. Even very thin cables with a cross-section of only 0.13mm2 and multi-strand cables for high-speed data transmission can also use ultrasonic welding technology.
Categories
latest blog
© Copyright: 2025 Hangzhou Altrasonic Technology Co.,Ltd All Rights Reserved
IPv6 network supported
Scan to WhatsApp