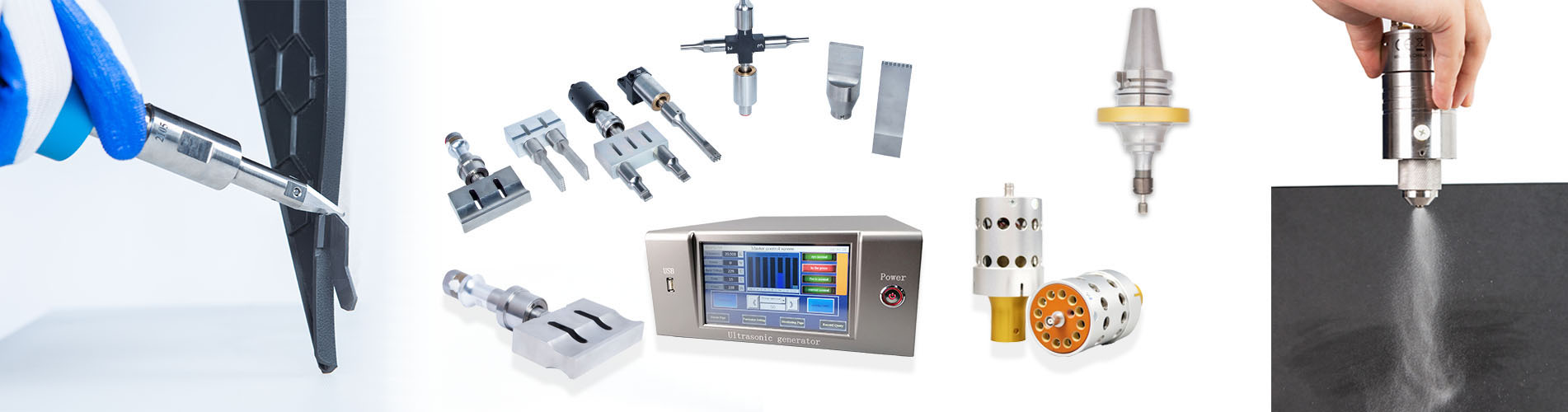
Application Of Plastic Welding Technology In The Automotive Industry
Application Of Plastic Welding Technology In The Automotive Industry
In modern vehicles, whether it is exterior decorative parts (such as bumpers, fenders, wheel covers, deflectors, etc.), interior decorative parts (such as instrument panels, door inner panels, sub-dashboards, glove compartment covers, seats) Chairs, rear guards, etc.), or functional and structural parts (fuel tank, radiator water chamber, air filter cover, fan blades, etc.), the shadow of plastic parts can be seen everywhere. At present, the plastic material of kg on modern cars replaces the traditional metal materials that originally required 200-300kg, and the weight-reducing effect is very prominent, which is of great significance for saving energy and reducing greenhouse gas emissions. For example, the replacement of metal by automobile plastic intake manifold can reduce the quality by 40% to 60%, and the surface light clear flow resistance is small, which can improve engine performance and play a certain role in improving combustion efficiency, reducing fuel consumption, vibration and noise reduction. According to statistics, there are dozens of plastics for automobiles, and the average amount of plastics per vehicle has accounted for 5% to 10% of the weight of automobiles. With the development of lightweight vehicles and the expansion of automotive plastics, automotive plastics The consumption of bicycles will further increase in the future.
There are two types of plastics for automobiles: one is a thermosetting plastic that can withstand ordinary baking operations; the other is a thermoplastic, which has the advantage of being easy and fast to process. Among the plastics for vehicles, the top 7 plastic materials and their proportions are roughly: 21% for polypropylene, 19.6% for polyurethane, 12.2% for polyvinyl chloride, 10.4% for thermoset composites, and ABS 8 %, nylon 7.8%, polyethylene 6%.
Plastic connections are a key part of their widespread use. The plastic can be joined by mechanical fastening, bonding or welding. The fast fastening connection is suitable for all plastics, but it is costly, stress-concentrated, does not form a sealed joint or achieves proper performance. Bonding provides excellent performance and high quality joints, but it is difficult to operate, requires careful joint and surface preparation, and is very slow and not suitable for mass production. The welding is economical, simple, fast and reliable, and can form joints with static strength close to that of the base metal, so it is suitable for mass production and has been increasingly used in the automotive industry. The level of plastic welding technology has become one of the indicators to measure the level of automotive production technology and the level of new material development.
Various plastic welding methods for the automotive industry
The welding of plastics is limited to the welding of thermoplastics, because only thermoplastics can melt or soften when heated, while thermosets cannot soften and remelt when heated.
Hot air welding is similar to metal oxyacetylene gas welding, except that the latter is heated by a hot gas stream with an open flame. In the hot gas welding process, the hot gas flow from the welding torch (typical temperature is 200-300 ° C, flow rate is 15 ~ 60 L / min) and the filling rod and the weldment are heated at the same time. When the surface of the material softens to a viscous state, the filling rod is continuous. Press into the weld. The filling rod material is the same as the base material, usually round (about 3mm in diameter), and multi-weld welding is used when welding thick plates. One disadvantage of circular filler rods is that hollow bubbles are easily trapped in the weld during multiple weld passes, resulting in reduced strength, which can be solved by using triangular section weld bars. Typical materials that can be hot air welded include polyvinyl chloride, polyethylene, polypropylene, plexiglass, polycarbonate, polyoxymethylene, polystyrene, nylon, ABS, and the like. The main advantage of hot gas welding is adaptability (flexibility), which can be used to process large, complex parts with simple portable equipment. Hot air welding is suitable for irregular structures, but it is slow, and the quality of the welding is largely dependent on the skill of the operator, so it is rarely used for mass production, but it is suitable for repair operations.
© Copyright: 2025 Hangzhou Altrasonic Technology Co.,Ltd All Rights Reserved
IPv6 network supported
Scan to WhatsApp