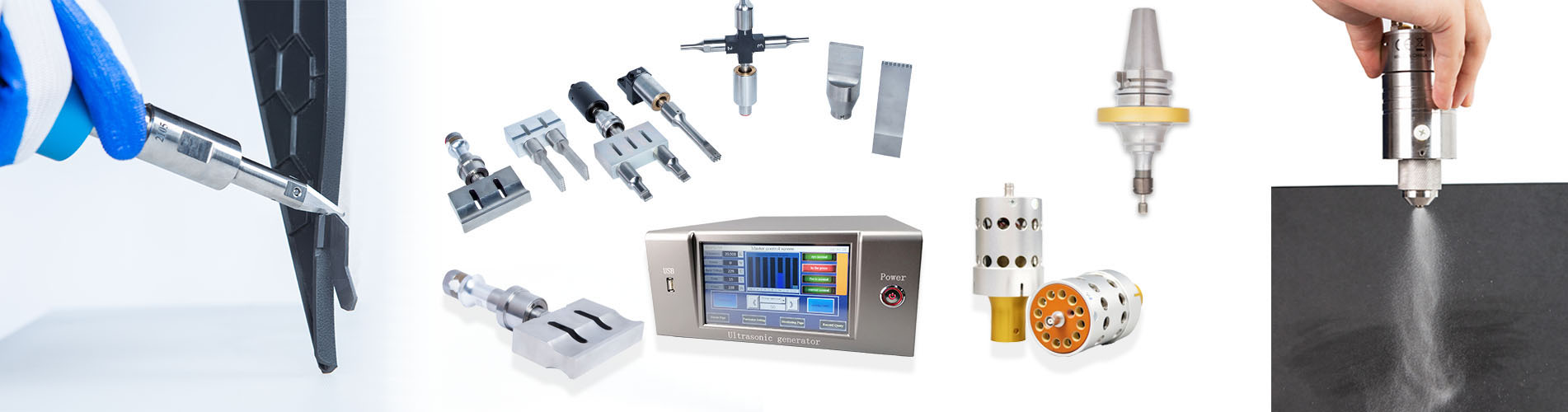
The application of ultrasonic technology in machining can be divided into two categories according to the characteristics of its processing technology. One is to use ultrasonic abrasive treatment with abrasives, such as ultrasonic hole processing, ultrasonic grinding, ultrasonic polishing, ultrasonic deburring and the like. The other is ultrasonic machining combined with cutting tools and other machining methods such as rotary ultrasonic drilling, grinding and milling. Ultrasonic electrochemistry, ultrasonic vibration cutting,
Item No.:
HS-M20Payment:
T/T, PayPal, WWestern UnionProduct origin:
ChinaShipping port:
Shanghai or Ningbo
20khz Ultrasonic Assisted Drilling Machining For CNC Machines
Specification:
Item No | HS-M20 |
Frequency | 20 kHz |
Power | 500 watt |
Voltage | 110V / 220V |
Power adjusting | Step or Continuous |
Working time control | 24 hours |
Application | milling, drilling |
Weight | 30 KG |
Generator | Digital |
Length of cable | 5 m |
Composition:
Power Source:
As we know, this machining process requires high frequency ultrasonic wave. So a high frequency high voltage power supply require for this process. This unit converts low frequency electric voltage (60 Hz) into high frequency electric voltage (20k Hz).
Magnetostrictive Transducer:
As we know, transducer is a device which converts electric single into mechanical vibration. In ultrasonic machining magnetostrictive type transducer is used to generate mechanical vibration. This transducer is made by nickel or nickel alloy.
Booster:
The mechanical vibration generated by transducer is passes through booster which amplify it and supply to the horn.
Tool:
The tool used in ultrasonic machining should be such that indentation by abrasive particle, does not leads to brittle fracture of it. Thus the tool is made by tough, strong and ductile materials like steel, stainless steel etc.
Tool holder or Horn:
As the name implies this unit connects the tool to the transducer. It transfers amplified vibration from booster to the tool. It should have high endurance limit.
Abrasive Slurry:
A water based slurry of abrasive particle used as abrasive slurry in ultrasonic machining. Silicon carbide, aluminum oxide, boron carbide are used as abrasive particle in this slurry. A slurry delivery and return mechanism is also used in USM.
Benefit:
1. The process is non-thermal, non-chemical, non-electric, leaving the chemical and physical properties of the workpiece unchanged. This low stress process provides high reliability for your critical applications.
2. Multiple features can be processed simultaneously at the wafer or substrate level and the process is scalable. Our processes are usually the highest quality and lowest cost solutions.
3. Ultrasonic machining features vertical sidewalls that allow you to retain valuable space for your design for increased productivity.
Workshop:
CE:
Packing&Shipping:
Shipping Port:Shanghai
Shipping Term:By express,by air,by ocean and so on.
Leading Time:Quick production leading time and fast delivery.Usually 1-3days if we have in stock.
Payment:
Previous :
Rotary Ultrasonic Processing for Drilling Carbon Ceramics Quartz GlassNext :
CAT 40 Knife Handle Rotary Ultrasonic Drilling For Hard And Brittle MaterialIf you are interested in our products and want to know more details,please leave a message here,we will reply you as soon as we can.
Categories
New Products
© Copyright: 2025 Hangzhou Altrasonic Technology Co.,Ltd All Rights Reserved
IPv6 network supported
Scan to WhatsApp