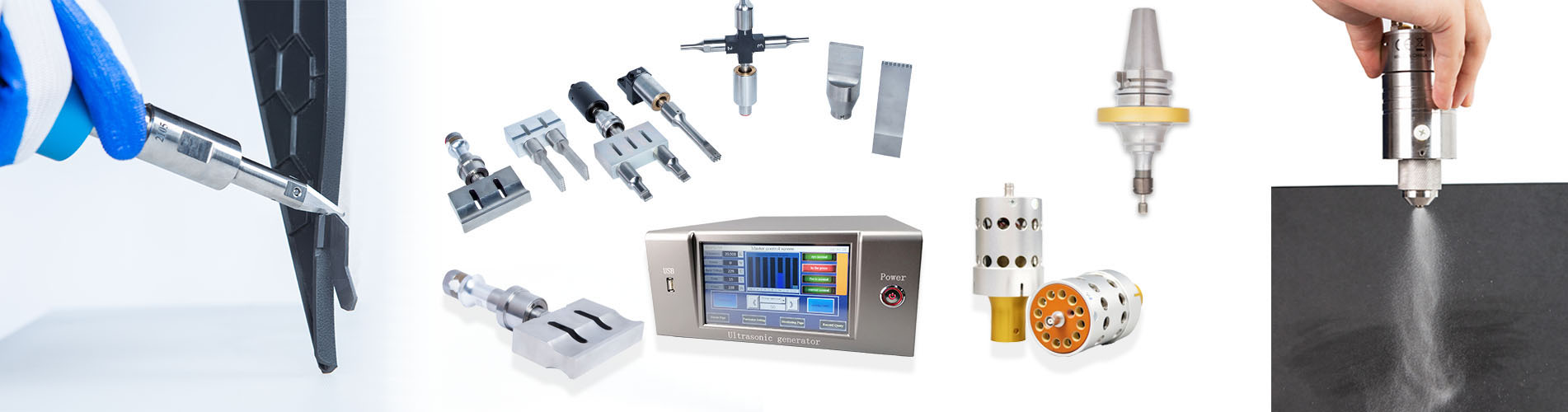
Ultrasonic milling is a kind of new method of process technology, is the ultrasonic vibration by adding high frequency micro-amplitude in general milling process, to change the machinable property of material. Ultrasonic milling device is constituted by generator, oscillator and horn.
Item No.:
HS-M2010Payment:
TT, West Union, PaypalProduct origin:
ChinaShipping port:
Shanghai20KHz Ultrasonic End Milling Equipment for Brittle Hard Materials Precise Processing
Specification:
Frequency |
20 Khz |
Output Power |
1000 W |
Voltage |
220 V |
Switch |
Handle or foot switch |
Power Adjusting |
Step or continuous |
Working Time Control |
24 Hours |
Weight |
30 KG ( Determined by the size of the horn ) |
Generator |
Digital Generator |
Ultrasonic milling
With the development of high speed spindle technology and ultrasonic power supply technology, the ultrasonic milling process gathering ultrasonic high frequency vibration and spindle rotating in high speed is regarded as the pioneer of high precision and high efficient process technology, applying in elaborate processing for various kinds of materials especially fragile rigid material. The milling process by using rotate milling cutter is suit for processing plane, groove, all kinds of form surface (such as spline, gear and thread) and special surface of mould.
Ultrasonic milling is proved as one kind of effective technology to improve the work ability of Titanium alloy, Aluminum alloy and stainless steel. The ultrasonic milling process has more advantages than traditional milling. Comparing the ultrasonic process effect among steel, Titanium alloy, Aluminum alloy and stainless steel, the most prominent surface quality improvement are Titanium alloy and Aluminum alloy, the most prominent cutting capability improvement is stainless steel, and the most prominent quality improvement in side work piece is steel.
Principle:
Ultrasonic machining process uses a power supply that converts conventional line voltage to 20KHz electrical energy.
This high-frequency electrical energy is provided to a piezoelectric converter that changes high frequency electrical energy into mechanical motion.
The ultrasonic motion from the converter is amplified and transmitted to the horn and cutting tool.
This causes the horn and attached cutting tool to vibrate perpendicularly to the tool face thousands of times per second with no side to side motion.
A recirculating pump forces E/Z Pump™ abrasive, suspended in a liquid medium, between the vibrating tool face and the workpiece. The abrasive particles strike the workpiece at 150,000 times their own weight.
These tiny abrasive particles chip off microscopic flakes and grind a counterpart of the tool face.
Applications
1. Various kinds of materials especially fragile rigid material.
2. Processing plane, groove, all kinds of form surface (such as spline, gear and thread) and special surface of mould.
3. Application area: machining industry, machine tool equipment manufacturing.
4. Application occasion: manufacturing enterprise, universities and colleges, scientific research institution, mechanical equipment transformation industry.
Technical Parameters:
Product shape: BT40 milling machine handle
Working frequency: 15-21KHz;
Resonance point amplitude: 10um or more;
Speed: 3000 r / min or less
Matching tool: carbide end mill head Φ2-Φ13; disk cutter Φ50;
Power: 1000W
Competitive Advantages:
· Virtually any hard material can be machined
· Little heat is produced
· Since the motion of the tool is up-and-down vibration rather than rotation as in traditional machining, the holes cut are not limited to circular shapes but can be any shape. Custom "cookie cutter" tools can cut complicated shapes.
· Good surface finish and higher structural integrity is obtained
Previous :
20khz Rotary Ultrasonic Maching Assited Machine for Milling and Wokpiece ProcessingNext :
20khz 1000W Ultrasonic Milling Machine with Rotating Multi End Milling Tool for Hard Metal CuttingIf you are interested in our products and want to know more details,please leave a message here,we will reply you as soon as we can.
Categories
New Products
© Copyright: 2025 Hangzhou Altrasonic Technology Co.,Ltd All Rights Reserved
IPv6 network supported
Scan to WhatsApp