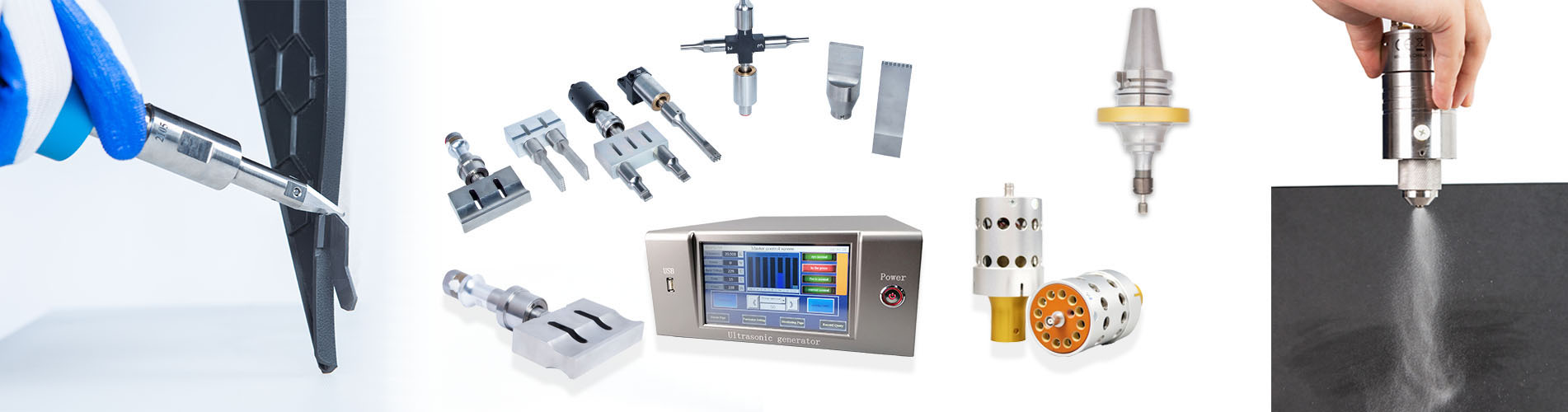
Ultrasonic wire harness welding machine welding action
Ultrasonic wire harness
welding machine welding action
The ultrasonic wire harness
welding machine tool is mainly composed of four parts: welding head, anvil
connecting block, anvil top block and polymerization module. When welding, the
wires are arranged vertically and tightly attached to the anvil connection
block. After the foot switch, the polymerization module moves toward the anvil
top block, and the anvil connection block is connected to the anvil top block
to move downwards, and the line is tight. Pressed in the weld zone, the weld
head vibrates and transfers energy to the copper wire, thereby welding the wire
harness together.
When welding, except for the
vibration of the welding head, the other tool heads are not moving. After the
welding is completed, the polymerization module is retracted, the anvil top
block is retracted, and the anvil connection block is raised, so that the wire
harness can be taken out. Since the welding head is vibrating, and the other
tool heads are fixed, in order to prevent welding between the tool heads and
the welding head, the welding machine is damaged, so the upper surface of the
welding head and the bottom surface of the polymerization module and the side
surface of the anvil top block are A gap of 0.025 mm is left on the side of the
anvil connection block so that the welding head cannot be in contact with other
tool heads.There should also be no debris such as broken copper between these
gaps, otherwise the working surface of the tool head will be corroded during
welding, and the circuit board may be damaged in severe cases.
Since the ultrasonic
vibration is generated by the welding head, the energy is transmitted from the
welding head to the anvil top block. Therefore, the closer the energy is to the
welding head, the more energy is transferred from top to bottom, so the line
should be thick. The wire is placed at the lowermost end, close to the welding
head surface, and the thinner wires are arranged vertically upwards in order,
so that the thick wire can obtain a large energy, thereby preventing
over-welding or insufficient welding. Vertical alignment prevents side
soldering and ensures soldering quality.
Ultrasonic welding
requirements for wire placement
When performing ultrasonic
welding, it is necessary to set relevant parameters such as wire
cross-sectional area, wire alignment, pressure, welding pitch, amplitude,
width, pressure, energy, and the like. During the welding process, the wires
should be vertically overlapped, and the large section lines should be placed
close to the welding tool head below to make the welding sufficient; the
conductors should be placed close to the anvil surface and close together to
make it strong enough after welding. The length of the conductor overlap is
generally set to 13 ~ 15 mm, the overlap length is too short, the welding
strength is not easy to guarantee, the overlap length is too long, the welding
tip is easy to form a lift, and the operation of the next process is
inconvenient. Oxidation, broken wires, defects and melting of the insulating
layer are not allowed on the surface of the welded surface.
Important parameters and
advantages of ultrasonic welding
1) Amplitude is the
maximum distance in the direction of vibration from the starting point of
vibration, in microns. They interact when welding, which directly affects the
welding quality of the wire. Different wires have different settings.
2) The surface of
the width polymerization module and the opposite surface of the anvil
connection block, the spacing between them during welding, in millimeters, the
size of which determines the width of the weld.
3) The pressure is
the pressure exerted by the anvil block on the copper wire of the weld zone.
The magnitude of the pressure is related to the gas pressure. The direction of
action is perpendicular to the direction of vibration, in pounds per square
inch.
4) The total energy
released by the welding machine during the energy welding process, in joules.
That is, when the energy released during welding reaches the set value, the
welding is completed.
Ultrasonic welding has its
unique advantages:
1 High welding strength,
excellent electrical conductivity after welding, extremely low or nearly zero
resistivity;
2 welding materials have
non-melting, non-fragile conductor characteristics;
3 short welding time,
greatly improved efficiency, fast, energy-saving;
4 welding process is stable,
On-line detection control;
5 does not need any gas,
solder, flux;
6 welding without sparks,
smoke, environmentally friendly and safe;
7 improve welding quality,
to ensure the reliability of the product conductor performance.
Ultrasonic wire harness
welding machine tooling
© Copyright: 2025 Hangzhou Altrasonic Technology Co.,Ltd All Rights Reserved
IPv6 network supported
Scan to WhatsApp