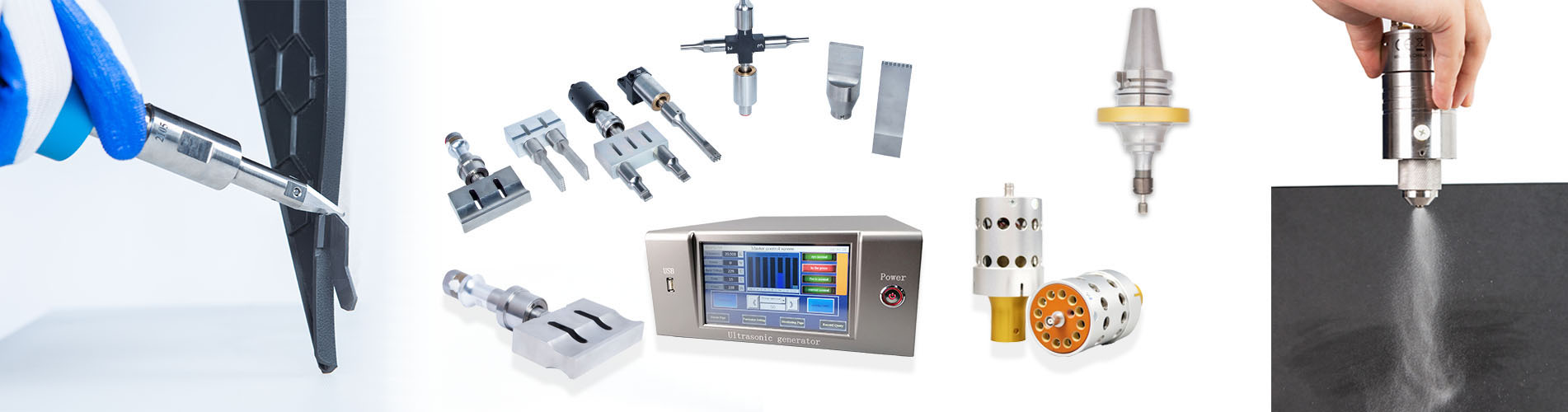
Ultrasonic Metal Welding
Ultrasonic metal welding is to transmit tens of thousands of high-frequency vibration waves per second to the surface of two metal workpieces to be welded, and then apply a certain pressure to make the metal surfaces rub against each other to form a fusion between the molecular layers, thusing achiving the purpose of welding.
Our ultrasonic metal welding machine uses frequency automatic tracking technology to change the mold and work without frequency tuning. It achieves a constant amplitude function and stepless adjustment of amplitude. Constant amplitude function ensures consistent welding.
Ultrasonic metal welding machines do not require pre-treatment of the surface to be welded and post-weld post-treatment as in other welding. Ultrasonic welding during processing does not require external factors such as flux, metal fillers, and external heating. Ultrasonic welding minimizes the temperature effect of the material (the temperature of the weld zone does not exceed 50% of the absolute melting temperature of the weld metal), so that it does not change the metal structure, so it is suitable for welding applications in the electronics field.
Advantages of ultrasonic metal welding:
1. It can weld two different materials
2. Do not destroy the metallographic structure of the material
3. Short welding cycle and high efficiency
4. Less heat generated relative to the solder joint, and does not affect other materials
5. The welding strength is almost close to its own strength
6. No other auxiliary welding materials are needed
7. Conductivity and resistance are not affected
8. Low energy consumption
Previous :
Ultrasonic Non-woven Fabric WeldingNext :
Ultrasonic Horn© Copyright: 2025 Hangzhou Altrasonic Technology Co.,Ltd All Rights Reserved
IPv6 network supported
Scan to WhatsApp