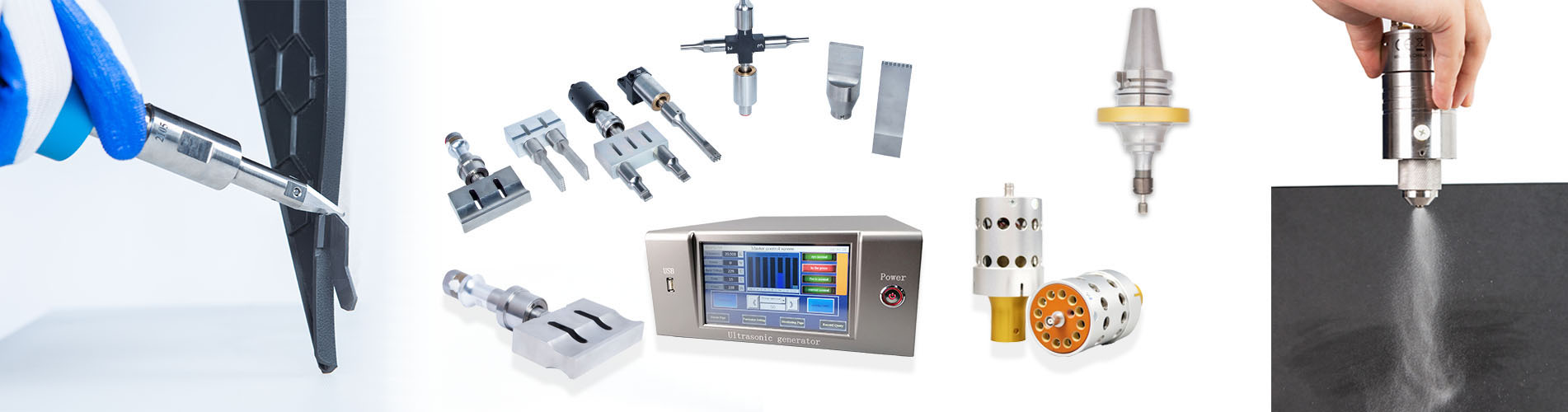
Ultrasonic degassing using in aluminum casting process
Any gas (unless intentionally blasted through the melt) is usually completely dissolved in the liquid metal and no free bubbles exist in the liquid volume. Therefore, the theory of ultrasonic degassing well developed for water (e.g. by Kapustina) is only applicable to the liquid metals after the cavitation starts to produce bubbles. In other words, it is only possible to produce the bubbles if the external energy supplied to the melt by ultrasound, creates conditions for heterogeneous nucleation of a bubble that can be filled with the dissolved gas.
According to a theory of acoustic degassing that Kapustina suggested for liquids, with existing vapor/gas bubbles, the degassing is controlled by the pulsating bubbles that accumulate dissolved gas due to its diffusion from the liquid in the rarefaction stage of bubble oscillation and recombination to the molecular form inside the bubble. The bubbles then grow, coalesce and eventually float to the surface. The role of cavitation according to Kapustina is in acceleration of the process due to multiplication of bubbles and more active diffusion of the dissolved gas into the small bubbles oscillating in a nonlinear manner. In addition, intense cavitation produces acoustic flows and secondary convective flows that contribute to bubbles distribution and flotation. Water is an example of such liquids, with oxygen bubbles readily present in the liquid volume. As a result, the degassing threshold for water (i.e. the sound intensity which leads to gas liberation from the liquid phase) is always lower than the cavitation threshold.
The situation, as has been pointed out by G.I. Eskin, is quite different for liquid metals, where vapor–gas bubbles do not usually exist and their formation requires cavitation of the liquid.In this case, the degassing and cavitation thresholds must coincide. The cavitation nuclei are of the same origin as the degassing nuclei and are represented by gas adsorbed onto the surface of poorly wetted inclusions. While the cavitation threshold shows the starting point of degassing, the degree of cavitation development determines the degassing in melts. In this process, the disruption of the dynamic equilibrium in the melt–oxide–hydrogen system by cavitation is strongly controlled by the concentration of solid oxide inclusions.
Liquid aluminium and its alloys react actively with gases, forming non-metallic impurities. One of the most important gases is hydrogen that finds the way to the liquid metal through the interface between the melt and the atmosphere. The main sources of hydrogen are: the molecular hydrogen in air and water moisture or vapor in the atmosphere. The latter reacts with liquid aluminium at the surface of the melt and produces alumina and hydrogen. The resultant atomic hydrogen is dissolved in the aluminium, and Al2O3 is deposited at the surface or dispersed in the liquid. Hydrogen that is not dissolved, or hydrogen that precipitates during degassing or solidification, forms molecular hydrogen. Water vapor can also react with liquid Al, producing molecular hydrogen as well; this will mostly dissolve back into the air.
The practical importance of dissolved hydrogen comes from the sharp decrease of its solubility with aluminium solidification: dissolved hydrogen can be measured up to 0.65 cm3/100 g in liquid aluminium just above the melting temperature, and just below the solubility drops down to 0.034 cm3/100 g. During solidification, this difference makes the excess hydrogen to precipitate and, being trapped between the solid dendrites, form porosity. Gas porosity combined with shrinkage porosity is detrimental to the mechanical properties of the final products, especially to the fracture toughness, fatigue endurance and ductility. Moreover, hydrogen that has not had time to precipitate and formed supersaturated solid solution with aluminium will precipitate during downstream processing, e.g. homogenization, extrusion or hot rolling, forming delamination and secondary porosity, especially harmful in thin gauge products or surface-critical applications.
Since 2000 the interest to ultrasonic degassing has significantly increased due to the environment and energy efficiency. A number of research groups around the world have been involved in the research.
© Copyright: 2025 Hangzhou Altrasonic Technology Co.,Ltd All Rights Reserved
IPv6 network supported
Scan to WhatsApp