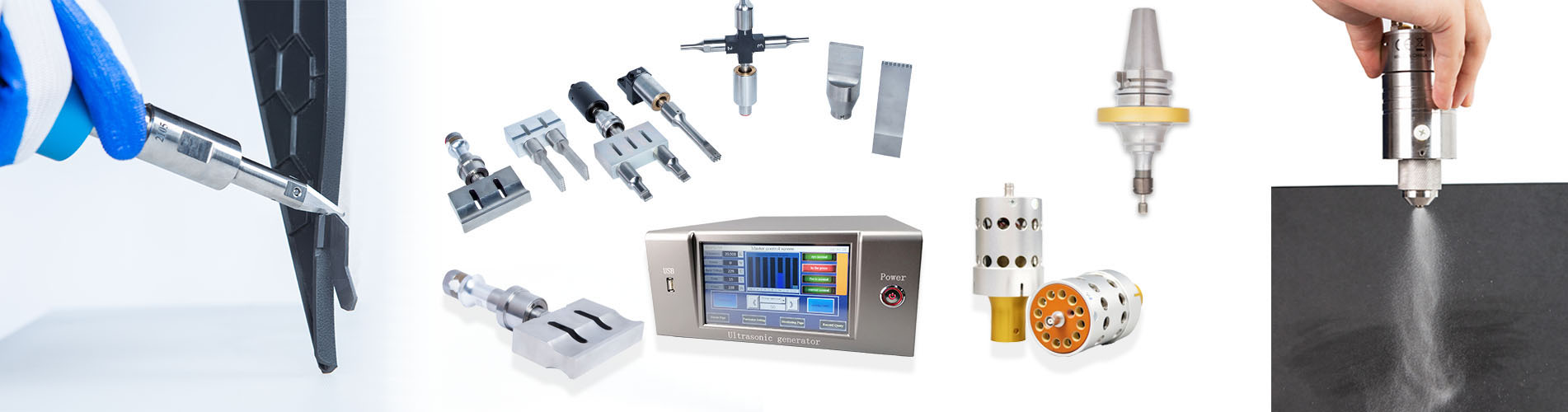
ROLE OF FIXURES IN ULTRASONIC PLASTIC WELDING-3
The fixture material choice will also affect how the plastic material flows at the joint interface. A soft resilient type of material will create a different flow rate than a rigid metal nest. Different fixture materials will create various frictional reactions at the weld joint. An experienced ultrasonic tool maker can assist with choosing the appropriate fixture material. Most of the time they will be right based upon their application experience and exposure to the broad choice of plastic material choices used to manufacture plastic products. Fortunately, if they select wrong it is rarely a life altering event.
Most fixtures include a slotted aluminum subplate for mounting to a welder base or automation system. The slotted subplate allows for ease of alignment between the part and the ultrasonic horn. Many fixtures will incorporate leveling features on the aluminum subplate to adjust the nest if the fixture in not parallel to the machine and the ultrasonic horn.
Just about any type of attachment can be added to an ultrasonic fixture to improve alignment, enhance part loading and unloading, eject the part, clamp parts, provide slides to move the part or the fixture, etc. Servo and pneumatic drive motion control systems have also been used as fixture attachment devices to lift the part to a stationary vibrating ultrasonic horn. Common used fixture attachments include the use of clamps and slides. A clamp is often used to provide support to the part, but allow a split fixture to open wide for part loading. This clamp approach allows the fixture to provide excellent support at the joint, but still open up for part loading. This fixture clamping approach is often necessary due to limited stroke capacity of the ultrasonic weld machine. Slides are also incorporated into fixture designs to move the part into a position out from under the ultrasonic horn to allow for part loading. Slides are also used for welding at different locations on the part, to move a fixture component into position for improved support and to scan along a weld seam. Slides have been used to move a part along an X-Y axis to aid in installation of multiple inserts or to allow the horn to stake posts at multiple locations. With the use of slides one finds other fixture attachments like stops and detents to control the motion position. The use of clamps and slides can be activated manually or automatically depending upon requirements for volume, ease of use and cost considerations. Mechanical part ejection attachments are often added to fixtures to enhance part removal after the ultrasonic welding process. This eject feature is generally required if there is a deep draw to the part or the part imbeds itself into the nest during the assembly process. The mechanical eject attachment components can be as simple as a manual lever lift or a little more complex like a lift driven by a pneumatic cylinder. Smart fixtures with plc controls have been used as a fixture attachment to provide sensors to ensure part placement before the weld cycle and to activate automatic part ejection after the weld cycle. It is feasible to envision that these smart fixtures could also incorporate part loading.
Customers that need rapid tool change are constantly requesting quick change fixtures. For quick change tooling, the use of dowel pins and bushings are commonly found fixture attachments. Coupled with quick tool change features for the ultrasonic transducer, booster and horn assembly, the end user has the capability to change jobs much faster providing a substantial reduction in setup time.
© Copyright: 2025 Hangzhou Altrasonic Technology Co.,Ltd All Rights Reserved
IPv6 network supported
Scan to WhatsApp