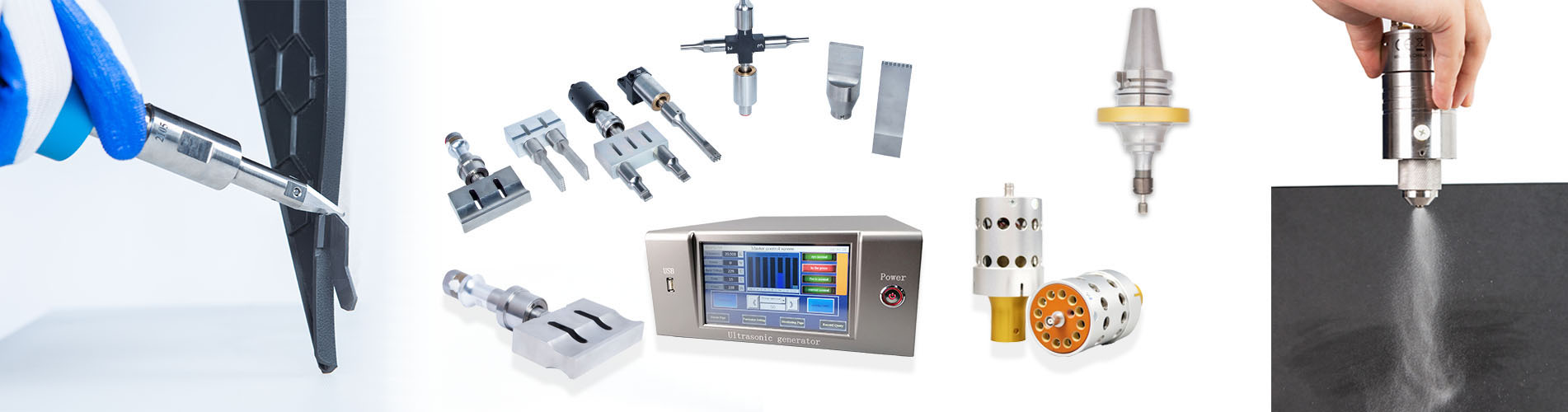
Multi-Head Ultrasonic Spot Welder for Felt in Automobile Coat and Hat Stand
The automobile coat rack felt
multi-head ultrasonic spot welding machine can also be called the automobile
coat rack assembly welding equipment, which refers to the welding of the main
body of the automobile coat rack with the EPDM+PP rubber strip, and the
ultrasonic position of the automobile coat rack has multiple places. For
welding, multiple ultrasonic systems can be used for switching welding, and if
necessary, a hand-held ultrasonic welding machine can be used for repair
welding.
Ultrasonic welding sample of car coat and hat stand
Automobile coat rack
felt multi-head ultrasonic spot welder. Every process of welding parts is
completed in three parts in one device (eight sets of generators). Twenty
solder joints are automatically divided into three parts. The whole frame is
welded and requires a beautiful appearance. No thorns, the color is painted,
the coating is uniform, the structure is reasonable; easy to operate, debug,
repair, easy to handle; all processing beats within 60 seconds (excluding pick
and place). The number of welding points of the coat racks designed by various
automotive interior parts manufacturers is different, and the relative
parameters are also different.
Ultrasonic welding
of car coat and hat rack
Solidify the plastic
well on the car coat rack
The ultrasonic wave
of automobile coat and cap frame adopts 28KHZ frequency system and titanium
alloy welding joint material: the front door is processed and made by titanium
alloy material. After professional ultrasonic mold software analysis, it can be
reproduced after qualified parameters such as frequency and amplitude, so as to
ensure uniform amplitude of the mold and improve service life.
Main function of multi - head ultrasonic spot welding machine
for auto coat and hat rack
More than using high strength steel as the framework, welding
head down welding, single welding head separation control at the same time,
each ultrasonic adopts air cooling device, the limit screw can adjust the
height of the upper die, controlled by the cylinder on the plate movement, PLC
man-machine interface control, convenient debugging, and adopting the side pull
structure installation, high precision. The whole machine is easy to debug and
stable in performance. The practical model can be adjusted at will, and can
also cooperate with semi-automatic or full-automatic production.
The pushing mechanism of the equipment can be divided into
manual operation and automatic operation, manual operation is a single action,
mainly used for the debugging of the mechanism and mold. In the PLC computer
touch screen on the main operation screen, according to the welding requirements
of the workpiece welding time, curing time, delay time, pressure value to set.
Press the computer touch screen to determine automatically,
close the door (the proximity switch indicator light is on) or the safety
grating, and press the start switch (blue) left and right buttons with both
hands. The process is controlled by PLC to achieve full automatic control.
Start the upper die of the switch to perform pressure welding on the workpiece.
Production for automatic, automatic control system using programmable
controller (PLC) to control, cylinder coherent motion. Simple operation,
reliable performance, compact size, improve production efficiency and quality.
© Copyright: 2025 Hangzhou Altrasonic Technology Co.,Ltd All Rights Reserved
IPv6 network supported
Scan to WhatsApp