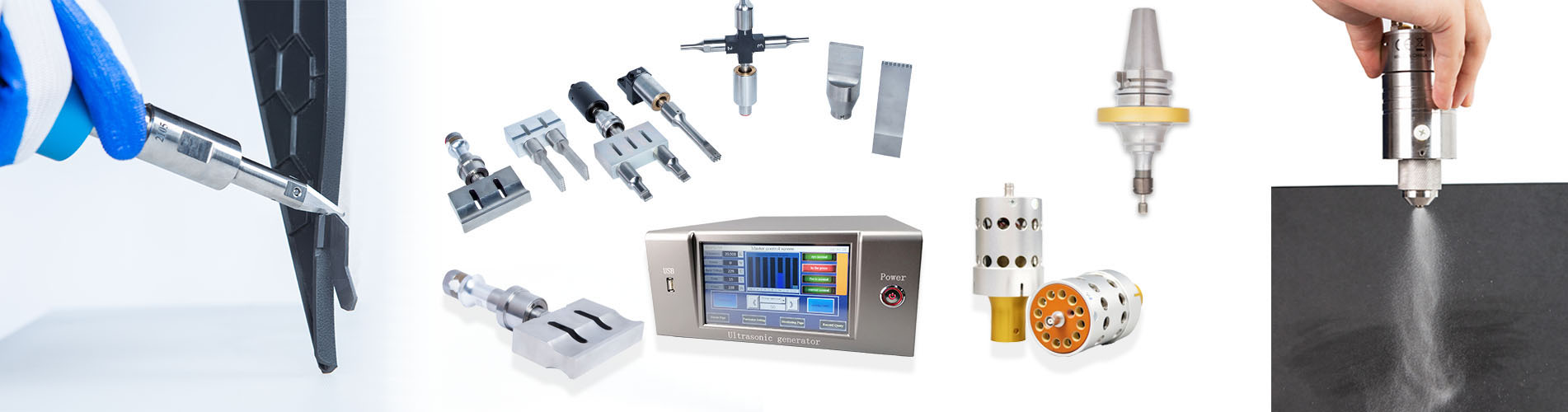
Medical industry welding program
Medical industry welding program
The ultrasonic welding form of the working end of the
polyethylene medical device belongs to the short-range welding (the distance
between the upper surface of the upper acoustic surface and the welding surface
is h<6.4mm), and the handle of the welding piece belongs to the remote
welding (h>64mm). The short-distance welding of polyethylene materials is
generally good, and the welding of long-distance welding is very poor.
In order to
improve the stability of the welding quality of polyethylene polyethylene
medical instruments, the Linggao LINGGAO ultrasonic welder is usually used to
design a stepped ultrasonic concentrator. The output amplitude is 30m, and the
amplitude of the concentrator is used to obtain polyethylene. The amplitude
requirements required for ultrasonic welding.
If
the welding pressure is too small, the heat generation will be insufficient,
resulting in partial non-fusion or long welding time, and the joint strength is
low; if the welding pressure is too large, the entire surface will be damaged
or crushed. Also, too long soldering time can cause such surface defects.
Therefore, the reasonable welding pressure of the working part of the
polyethylene medical device is 0.1 MPa, and the welding time is 0.7 s. For the
shank, due to the small welding surface area, the experimentally determined
reasonable ultrasonic welding pressure is 0.07 MPa, and the welding time is 0.7
s.
Polyethylene medical devices have a low surface hardness and must be properly protected against the surface of the product, otherwise surface dirt, surface indentations and burning may occur. Especially in the area where the upper acoustic pole edge is in contact with the weldment, the collapse caused by the local melting ten ultrasonic impact is more obvious, which greatly affects the appearance quality of the product.
Since ultrasonic welding is the last step before the product is formed, the appearance quality of the weldment is as important as the joint strength. Therefore, the use of the paper between the upper weldment surface and the upper acoustic extreme surface reduces the upper acoustic extreme surface (the upper acoustic pole material is generally an aluminum alloy) to the surface of the product, on the other hand, the reduction is also reduced. Surface indentation and collapse.
© Copyright: 2025 Hangzhou Altrasonic Technology Co.,Ltd All Rights Reserved
IPv6 network supported
Scan to WhatsApp