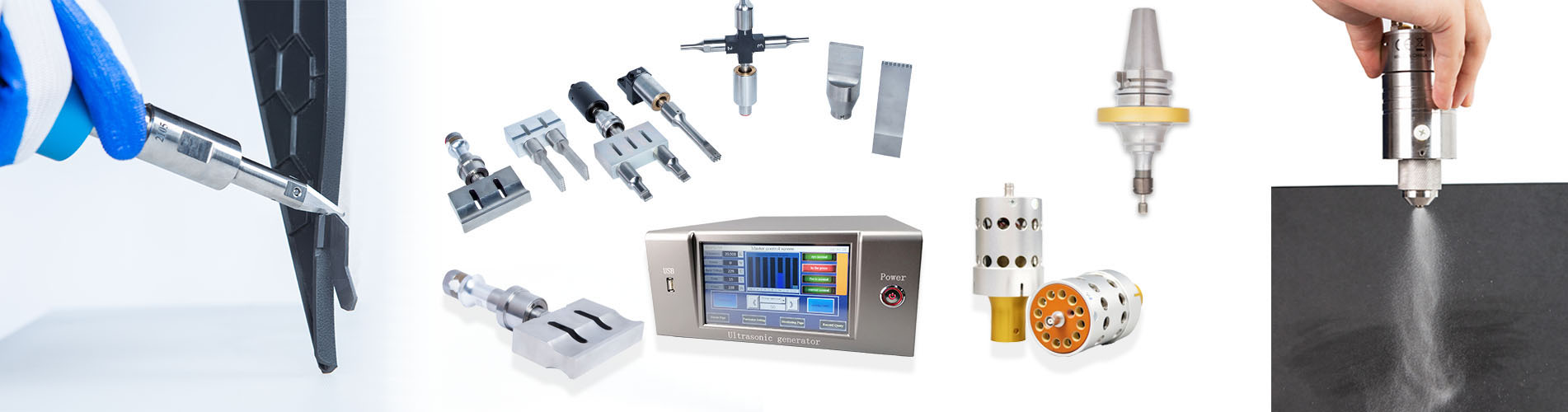
Laser Welding VS Ultrasonic Metal Welding
Solar panel
welding:
Laser
Welding VS Ultrasonic Metal Welding
First
round: Product aesthetics
Laser welding
uses a high-energy laser to melt the weld metal to create a joint. In the solar
heat absorbing plate welding, welding is performed in the form of a solder
joint with a spacing of 3-5 mm. Laser welding does not require pressurization
on the workpiece, the overall deformation is small, and the surface damage to
the heat absorbing layer is small. Ultrasonic metal welding causes wave
deformation on the surface of the sheet due to pressure. Although surface
deformation can be avoided by surface embossing, a weld mark of about 3 mm is
formed on the surface of the solar heat absorption. Therefore, the appearance
of products using laser welding is better than that of ultrasonic metal
welding. This round of competition, laser welding is better than ultrasonic
metal welding.
Second
round: Persistence
The welding
strength of laser welding is poor. When the hot and cold alternates frequently
or is subjected to external force, the solder joint is easy to break.
Ultrasonic metal welding is to superimpose two objects to be welded by vertical
pressure, combined with ultrasonic vibration and pressure to form a solid
connection. The bonding time is short and the joint part does not produce
casting structure defects, so the welding position is uniform and stable, and
the ultrasonic metal. There was no fracture after the 90 degree vertical
bending test. This round of competition, ultrasonic metal welding is better
than laser welding.
Third
round: Thermal conductivity
Laser welding
can change the physical structure of the object being welded, thus affecting
its electrical or thermal conductivity. Moreover, the laser welding results in
a small heat conduction area between the metal piece of the solar collector and
the copper tube, which affects the heat conduction efficiency. Ultrasonic metal
welding does not have this problem. Ultrasonic welding minimizes the
temperature effects of the material and does not alter the metal structure.
Therefore, the electrical conductivity or thermal conductivity after welding is
excellent, and the electrical resistivity is extremely low or nearly zero.
Ultrasonic metal welding has become the best choice for welding conductive and
thermal conductive materials. This performance can obviously produce laser
welding on flat solar collectors. The advantage that cannot be achieved.
According to the test, the ultrasonic metal welding product is about 3% higher
than the laser welding conduction efficiency (that is, the water temperature is
about 3% under the same working condition). This round of competition,
ultrasonic metal welding is significantly better than laser welding.
Fourth
round: Energy
consumption
As a
representative product of low-carbon energy-saving and environmental
protection, solar water heaters are widely recognized by the society and
consumers, and energy consumption indicators in the production process are also
receiving much attention. Welding of solar collectors is one of them. From the
comparative analysis of the welding principle, it can be known that ultrasonic
metal welding can minimize the temperature effect of the material (the
temperature of the weld zone does not exceed 50% of the absolute melting
temperature of the weld metal), so that the metal structure does not change, so
it does not It will anneal metal workpieces without cooling water. In terms of
energy consumption, ultrasonic welding can be performed between the same metal
and different kinds of metals, which is much less energy-consuming than laser
welding. This round of competition, ultrasonic metal welding is better than
laser welding.
Fifth
round: Cost
1. Cost
of equipment: internationally, the price of ultrasonic welding machine and
laser welding machine is equivalent. The procurement cost of single equipment
of ultrasonic metal welding machine is lower than that of laser welding
machine. The procurement ratio of the two is usually 300,000: 10,000. (Now the
price of domestic laser welding machines is also rapidly declining, about to
about 700,000) The laser welding machine generally has two laser welding heads,
and the ultrasonic machine generally has one welding head. For the same
production capacity, two ultrasonic welding machines are compared with one
laser welding machine.
2. Cost of use: Firstly, laser welding is suitable for thick materials, such as welding aluminum. The thickness of aluminum plate is generally chosen to be 0.4mm, while ultrasonic welding is suitable for thin products, such as aluminum plate, generally 0.2-0.3mm. In terms of welding materials, ultrasonic is superior. Secondly, the cost of consumables, the consumables for laser welding are xenon lamps and filter cartridges, and the ultrasonic consumables are welding heads. In general, laser welding consumables are cheaper than ultrasonic.
© Copyright: 2025 Hangzhou Altrasonic Technology Co.,Ltd All Rights Reserved
IPv6 network supported
Scan to WhatsApp