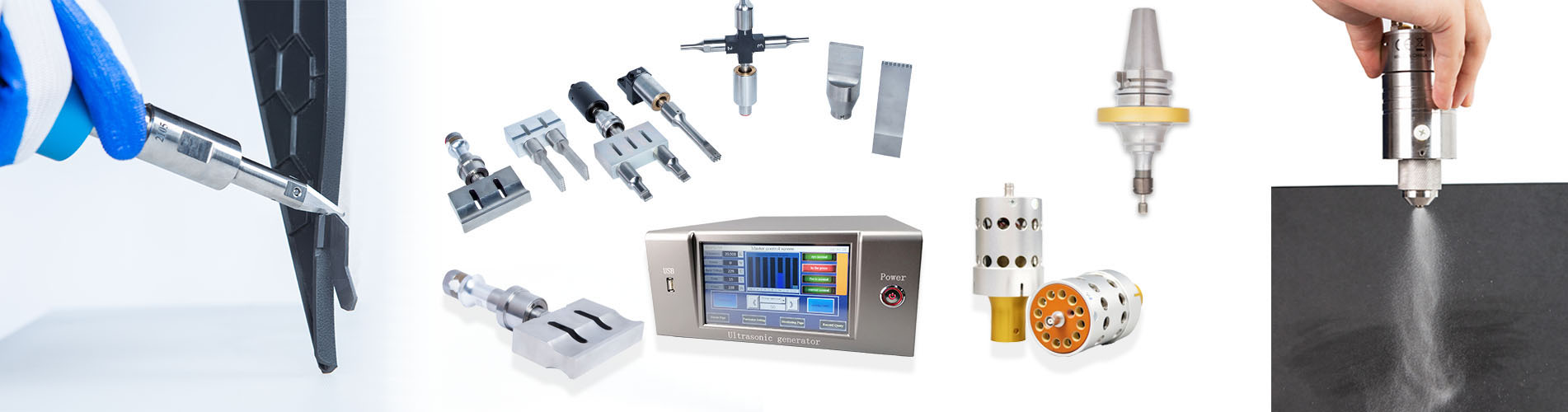
Intelligent control for Ultrasonic Welding
Alot can happen in 0.5 second, especially in the world of assembly. One or more rivets can be simultaneously inserted. Multiple beads of adhesive can be dispensed. And two thermoplastic pieces can be ultrasonically welded into a usable part.
For more than 30 years, ultrasonic welding has been a popular method for assembling parts made of amorphous or semicrystalline thermoplastic or thermoplastic composites. Ultrasonic welding is a form of friction welding that joins parts together by vibrating them against each other.
All ultrasonic welders feature a power supply (generator), computer controller, actuator (driven by a pneumatic cylinder or servo-driven ballscrew), transducer, booster and sonotrode horn. The transducer, booster and horn make up the ultrasonic stack.
Power is sent to the transducer, which contains piezoelectric crystals that expand and contract. This action causes mechanical vibrations that the booster increases and transfers to the horn, which, in turn, transfers ultrasonic energy to the joint interface.
Heat is generated at the joint through a combination of friction and hysteresis. The heat melts a small amount of plastic on each part. When the ultrasonic vibrations stop, the molten material solidifies and the weld is achieved. Actual weld time is usually between 200 and 400 millisecond
Besides speed, manufacturers like that ultrasonic welding is clean and economical, especially for small parts. They also like that suppliers are developing machines that give them more process control and the ability to weld complex plastic parts
To find a professional ultrasonic welding solution?
Click Altrasonic Welding to realize it !
© Copyright: 2025 Hangzhou Altrasonic Technology Co.,Ltd All Rights Reserved
IPv6 network supported
Scan to WhatsApp