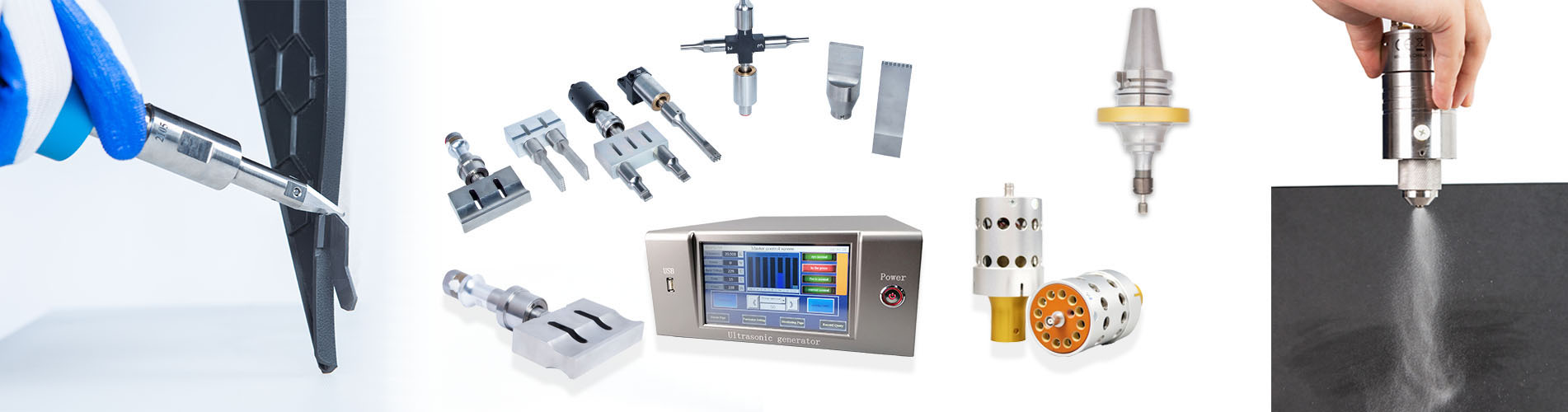
Analysis Of Ultrasonic Welding Equipment For Automobile Wiring Harness
Analysis of ultrasonic welding equipment for automobile wiring harness
The current production process of automobile wiring harness welding mainly includes crimping and ultrasonic welding: crimping is the use of terminals to press multiple wires together to form a joint; ultrasonic welding is the use of physical effects generated by ultrasonic vibration to combine the wires. The application of ultrasonic in the production of automotive wiring harnesses has become popular in Europe and the United States, mainly due to the development of ultrasonic metal welding technology.
Comparison of two technologies:
1. Crimping Advantages:
The production speed is fast; the equipment is simple. Disadvantages: there is a risk of rebound in metal stamping; there is a risk of oxidation and rust under severe working conditions, all risks can lead to poor contact.
2. Ultrasonic welding advantages:
Super electrical connection characteristics (basically zero resistance); insensitive to the risk of oxidation and rust in harsh working conditions. Disadvantages: equipment is expensive; consumables are also expensive.
What are the parameter adjustment, testing and analysis in the ultrasonic harness welding machine? Adjustable and detectable parameters: amplitude, pressure, welding time, welding energy, welding height, welding width.
Amplitude: The determination of the amplitude is firstly based on the mechanical properties of the material to be welded. The softer the material, the lower the required amplitude; secondly, according to the cross-sectional area of the welded wire, the larger the cross-sectional area, the thicker the welding thickness. Consider the ultrasonic in the welding direction Therefore, the larger the cross-sectional area, the higher the amplitude. The same machine, when welding 3mm² and 25mm² wire harnesses, the amplitude parameters are basically different by about 30% (so if the ultrasonic equipment does not have the function of continuously adjustable amplitude, how can it be adapted to wire harness welding?).
Pressure: The larger the cross-sectional area, the higher the welding pressure. Good equipment is digitally controlled by electrical proportional valves.
Welding width: According to the IPC standard and the German Volkswagen standard VW60307-CN-2005, the wire junction width to thickness ratio is between 1:1 and 2:1. The larger the cross-sectional area, the closer the junction width and thickness is 2:1. So when we get a wire harness product, first determine the welding width according to this rule; then determine the approximate welding height according to the width. High-quality welding machines use stepping motors or servo motors to adjust the welding width.
The welding time and welding energy should be determined by trial welding according to the cross-sectional area of the welding wire.
The height parameter is an important analysis parameter: when we determine the welding width, according to the previous analysis, the height value can be calculated. The height before and after welding can be used as the criterion for whether the line is missing before welding and whether the welding is good. . Quality analysis mainly refers to a high degree of judgment; of course, welding energy consumption and time can be used as additional constraint parameters to see if it exceeds the range. General practice: Set a height value (which can be calculated and determined by actual test welding), and then set the deviation value. When the height deviation exceeds the range, it can be judged as unqualified. This is true both before and after welding.
© Copyright: 2025 Hangzhou Altrasonic Technology Co.,Ltd All Rights Reserved
IPv6 network supported
Scan to WhatsApp