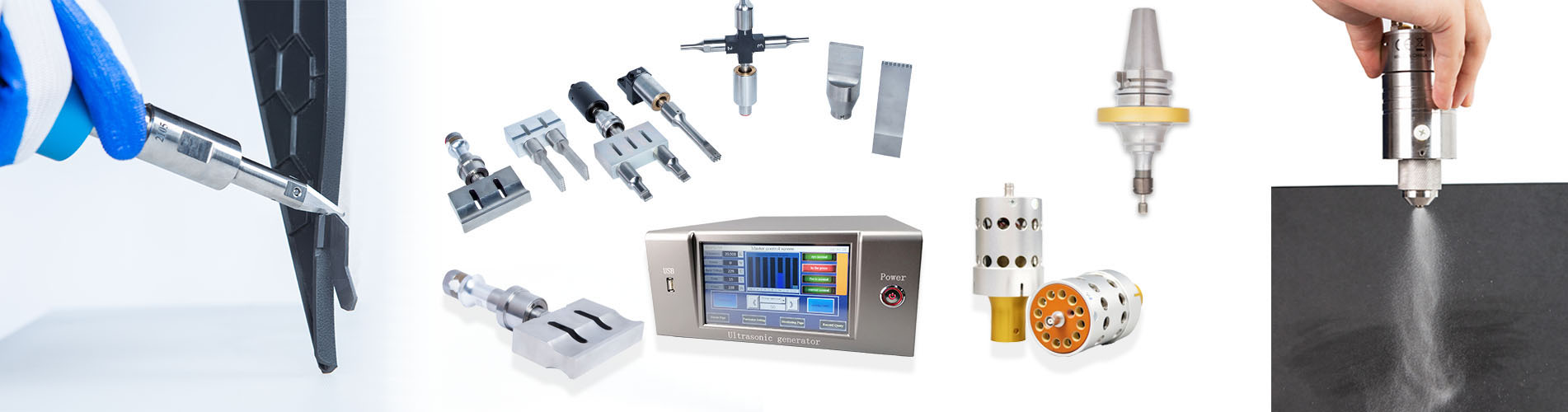
Place of Origin:Zhejiang, China
Brand Name:Altrasonic
Condition:New
Voltage:220V
Frequency:35kHz±500Hz, 35kHz±500Hz
Welding Area:OEM
Dimensions:440mmx205mmx140mm
Usage:Plastic Welding
Warranty:1 Year, One Year
After-sales Service Provided:Free spare parts, Online support, Video technical support
Key Selling Points:Long Service Life
Applicable Industries:Machinery Repair Shops, Manufacturing Plant, Other
Weight (KG):68 KG
Power (kW):1200W
Marketing Type:Hot Product 2023
Machinery Test Report:Provided
Video outgoing-inspection:Provided
Product name:Ultrasonic Plastic Welding Machine
Application:Plastic Welding
Certificate:CE
Horn working face size:10mm in diameter
For Application Range:PVC PP PPR PE EVA ABS
Power supply:220V, 50HZ, 10A.
Item No.:
HS-W35APayment:
T/T, West union, PaypalProduct origin:
ChinaShipping port:
Hangzhou or ShanghaiLead Time:
7
35khz Ultrasonic Plastic Welding Machine
Specification:
Item No | HS-W35A |
Frequency | 35kHz |
Power | 1200W |
Dimensions |
440mmx205mmx140mm |
Horn working face size |
10mm in diameter |
For Application Range |
PVC PP PPR PE EVA ABS |
Power supply |
220V, 50HZ, 10A. |
Description:
Ultrasonic welding equipment fit the exact specifications of the parts being welded. The parts are sandwiched between a fixed shaped nest (anvil) and a sonotrode (horn) connected to a transducer, and a ~20 kHz low-amplitude acoustic vibration is emitted. (Note: Common frequencies used in ultrasonic welding of thermoplastics are 15 kHz, 20 kHz, 30 kHz, 35 kHz, 40 kHz and 70 kHz). When welding plastics, the interface of the two parts is specially designed to concentrate the melting process. One of the materials usually has a spiked energy director which contacts the second plastic part. The ultrasonic energy melts the point contact between the parts, creating a joint. This process is a good automated alternative to glue, screws or snap-fit designs. It is typically used with small parts (e.g. cell phones, consumer electronics, disposable medical tools, toys, etc.) but it can be used on parts as large as a small automotive instrument cluster.
Advantage:
1. Ergonomic design
2. Can be controlled manually, or by foot switch
3. The blade is not sharp, safe and durable
Equipment maintenance:
1. Attention should be paid to the following matters when repairing ultrasonic generator (driving power supply).
Turn off the vibration power supply and remove the power plug. Remove the cover and discharge the large electrolytic capacitor. There is also high voltage residual electricity on the transducer. It should also be discharged (directly connected to the positive and negative poles with wires).
2. grounding to be thorough.
3. Confirm whether the power switch is OFF before connecting the power plug.
4. In order to prevent hearing damage during vibration, the processor should use hearing protector.
Previous :
Ultrasonic Plastic Welding Machine 15khz 20khz 35khz For Thermoplastic MaterialsNext :
15khz 20khz 35khz 2600W PSA Grading Cf Cards PVC PP PPR PE EVA ABS Slab Bottle Toy Welder Ultrasonic Plastic Welding MachineIf you are interested in our products and want to know more details,please leave a message here,we will reply you as soon as we can.
Categories
New Products
© Copyright: 2025 Hangzhou Altrasonic Technology Co.,Ltd All Rights Reserved
IPv6 network supported
Scan to WhatsApp