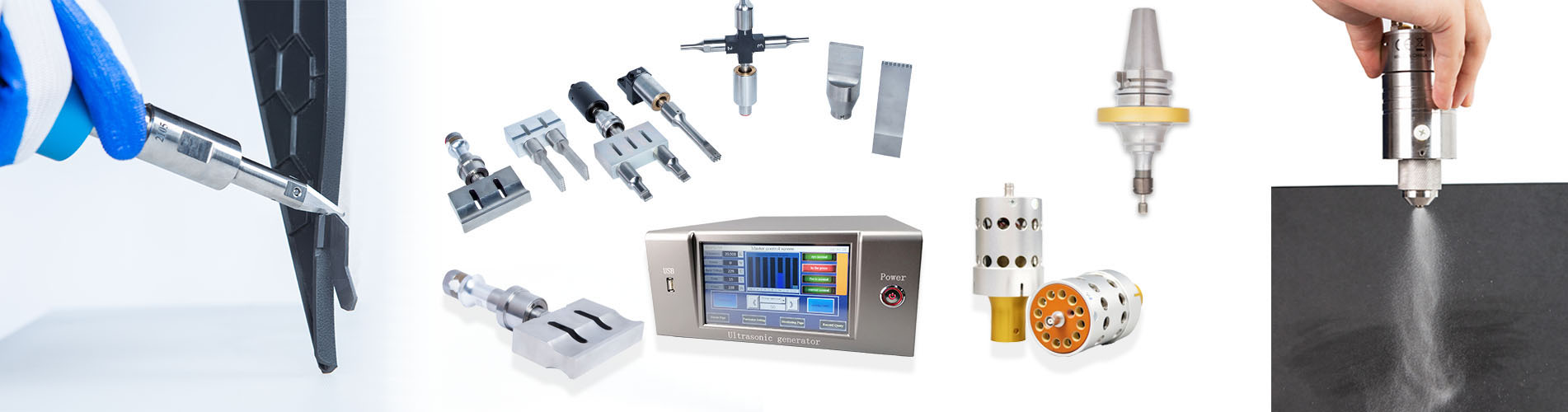
How Dose Ultrasonic Welding Work
In the 1982 musical comedy "Victor Victoria", Julie Andrews sang a high profile at the end of her character’s Paris cabaret show. She held up the notes, and the champagne glasses in the entire room shattered. This is a good illustration of how high pitch or high frequency sounds separate materials. But did you know that you can use high-frequency sound to bond materials together? Ultrasonic welding technology is used to assemble products in many industries-from medical equipment to sports shoes to cars.
Generally, you can use fasteners such as nails, screws, or threads to bond the material. This applies to metal, wood, fabric and plastic. For many plastics, glue is used. The glue forms a chemical bond between the glue itself and the surface of the plastic material that is bonded. Metals can be held together by heating other metals as adhesives, such as lead solder in electrical connections. Alternatively, the metals can be directly melted (welded) together; once the molten metal surface cools, the metals will bond together. Welding usually requires an open flame or torch to reach the high temperatures required to melt the metal surfaces together. Therefore, for some manufacturing tasks, this can be an expensive process.
The basic process of ultrasonic welding can be described by the following steps:
1. The part to be welded is placed in an anvil or fixture.
2. The horn is in contact with the part to be welded.
3. Apply pressure to keep the welding head in contact with the welding material and hold it together.
4. The horn emits ultrasonic vibrations to heat the material. The vibration moves up and down or left and right by less than one millimeter.
5. These materials are welded together.
6. The horns will retract and the welding material can be removed from the anvil.
The welding time, applied pressure and temperature are controlled by the computer or microprocessor in the welding equipment. What actually happens during welding depends on the nature of the material. In metal, ultrasonic vibration is transmitted parallel to the plane of the material. The frictional heat raises the temperature of the metal surface to about one-third of the melting temperature, but it does not melt the metal. Instead, heat removes metal oxides and thin films from the surface. This allows metal atoms to move between the two surfaces and form bonds that hold the metal together.
In the case of plastic, the vibration is perpendicular to the plane of the material, and frictional heat raises the temperature enough to melt the plastic. Plastic molecules mix together and form bonds. After cooling, the plastic surfaces are welded together. The welding time can vary, but the welding can be formed in as little as 0.25 seconds.
The influencing factors of ultrasonic welding include the frequency of the sound wave (usually 20, 30, or 40 kHz), the pressure to hold the material together, and the time to apply the ultrasonic wave (a fraction of a second or even more of a second).
Compared with traditional methods, ultrasonic welding has many advantages. First, compared to other methods, welding is performed at low temperatures. Therefore, manufacturers do not need to spend a lot of fuel or other energy to reach high temperatures. This makes the process cheaper. It is also faster and safer.
Ultrasonic welding does not require flammable fuel and open flames, so it is a safer process compared to other welding methods. Workers must not come into contact with flammable gases or toxic solvents. In electronic products, copper wires are usually connected to electrical contacts on the circuit board through solder. Using ultrasonic welding can accomplish the same task in a short time without exposing workers to the fumes of the negative lead solder. Although exposure to high-frequency sounds may damage the hearing of workers, this potential hazard can be easily reduced by putting the ultrasonic welding machine in a safety box or cage and/or using earmuffs.
Finally, ultrasonic welding is as strong and durable as conventional welding of the same material-this is just one of the reasons why this method is used in automobile manufacturing. In order to make cars lighter and more fuel-efficient, automakers are using aluminum as the main body metal. Compared with traditional welding, ultrasonic welding can be used to bond metals in a shorter time and at a lower temperature.
© Copyright: 2024 Hangzhou Altrasonic Technology Co.,Ltd All Rights Reserved
IPv6 network supported
Scan to wechat