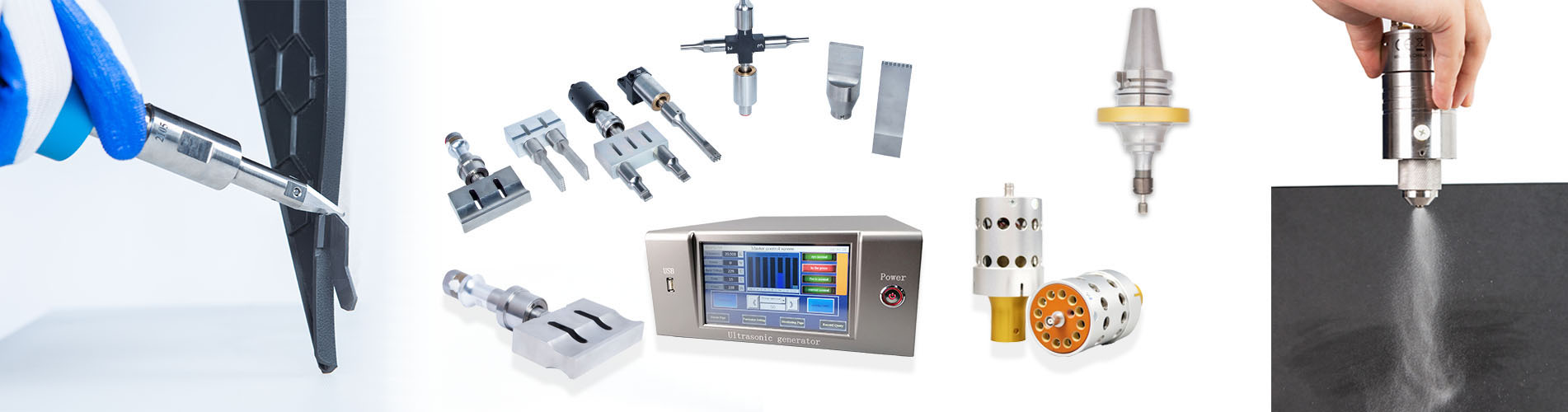
We supply High-power Ultrasonic Liquid Processors ,Substantial intensity of ultrasound and high ultrasonic vibration amplitudes are required for many processing applications, such as nano-crystallization, nano-emulsification, deagglomeration, extraction, cell disruption, as well as many others.
Product origin:
ChinaProduct weight:
17Kg
High-power Ultrasonic Liquid Processors Ultrasonic Cavitation in Water
Minimum Order Quantity: |
1 Set |
Price: |
|
Packaging Details: |
Foam case |
Delivery Time: |
In 7 Working Days |
Payment Terms: |
T/T, WESTERN UNION |
Supply Ability: |
100 Sets/Month |
Quick Detail:
Simple, low-cost design
Low operating costs
High efficiency
Low maintenance
Faster emulsification
Description:
We supply High-power Ultrasonic Liquid Processors ,Substantial intensity of ultrasound and high ultrasonic vibration amplitudes are required for many processing applications, such as nano-crystallization, nano-emulsification, deagglomeration, extraction, cell disruption, as well as many others. Commonly, a process is first tested on a laboratory scale to prove feasibility and establish some of the required ultrasonic exposure parameters. After this phase is complete, the process is transferred to a pilot (bench) scale for flow-through pre-production optimization and then to an industrial scale for continuous production. During these scale-up steps, it is essential to make sure that all local exposure conditions (ultrasonic amplitude, cavitation intensity, time spent in the active cavitation zone, etc.) stay the same. If this condition is met, the quality of the final product remains at the optimized level, while the productivity is increased by a predictable "scale-up factor". The productivity increase results from the fact that laboratory, bench and industrial-scale ultrasonic processor systems incorporate progressively larger ultrasonic horns, able to generate progressively larger high-intensity cavitation zones and, therefore, to process more material per unit of time. This is called "direct scalability". It is important to point out that increasing the power capacity of the ultrasonic processor alone does not result in direct scalability, since it may be (and frequently is) accompanied by a reduction in the ultrasonic amplitude and cavitation intensity. During direct scale-up, all processing conditions must be maintained, while the power rating of the equipment is increased in order to enable the operation of a larger ultrasonic horn
Applications:
Ultrasonic in the biochemistry of the earliest applications should be used ultrasonic to crush the cell wall, to release its contents. Subsequent studies showed that, low intensity ultrasonic can promote the biochemical reaction process, such as ultrasonic irradiation can increase the speed of liquid nutrition growth of algal cells, making the cells to produce proteins increased 3 times.Energy density and cavitations bubble collapse of ultrasonic field energy density, energy density is enlarged trillion times, great concentration caused by energy; sound chemistry led to the phenomenon of extreme heat and pressure cavitations effect of luminescence, is unique in form of exchange of energy and substance of sonochemistry. Therefore, ultrasonic chemical extraction, biodiesel production, organic synthesis, governance microorganisms, degradation of toxic organic pollutants, the chemical reaction speed and yield, the catalytic efficiency, biological degradation, ultrasonic anti fouling, biological cell crushing, dispersion and agglomeration, and the chemical reaction is more and more important role.
Specifications:
Model |
S-P20-1000 |
S-P20-1500 |
S-P20-2000 |
S-P20-3000 |
Frequency |
20±1 KHz |
20±1 KHz |
20±1 KHz |
20±1 KHz |
Power |
1000 W |
1500 W |
2000 W |
3000 W |
Voltage |
220±10% V |
220±10% V |
220±10% V |
220±10% V |
Temperature |
300 ℃ |
300 ℃ |
300 ℃ |
300 ℃ |
Pressure |
35 MPa |
35 MPa |
35 MPa |
35 MPa |
Intensity of sound |
>20 W/cm² |
>30 W/cm² |
>40 W/cm² |
>60 W/cm² |
Max Capacity |
> 10 L/Min |
> 15 L/Min |
> 20 L/Min |
> 30 L/Min |
Material Of Tip Head |
Titanium Alloy |
Titanium Alloy |
Titanium Alloy |
Titanium Alloy |
Competitive Advantage:
1.Save mixing time 20%~60%
2.Lower temps 30%~60%(30℃)
3.Less methanol 5%~30%
4.Less chemical (KOH) less 20%~50%
5.Total production cost save 15%~50%
6.Another benefit is the time of glycerol separation.This is also faster and one of the reasons for it is that less methanol is been used,so glycerol separation is faster.
Previous :
Ultrasonic Molten Aluminium Treatment SystemNext :
Supercritical Fluid Extraction Assisted By Ultrasonic Extraction EquipmentIf you are interested in our products and want to know more details,please leave a message here,we will reply you as soon as we can.
Categories
New Products
© Copyright: 2025 Hangzhou Altrasonic Technology Co.,Ltd All Rights Reserved
IPv6 network supported
Scan to WhatsApp